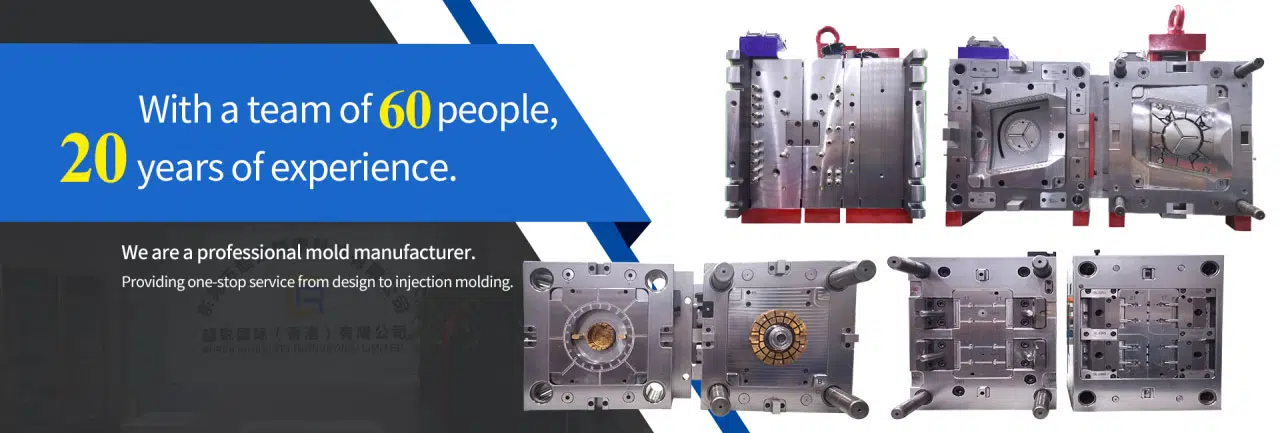
# Die Casting Process Overview
## What is Die Casting?
Die casting is a metal casting process that involves forcing molten metal under high pressure into a mold cavity. The mold cavity is created using two hardened tool steel dies which have been machined into shape and work similarly to an injection mold during the process.
## The Die Casting Process Steps
### 1. Clamping
The first step involves preparing and clamping the two halves of the die. Each die half is cleaned and lubricated to facilitate proper ejection of the casting. The lubrication time increases with part size, as well as the number of cavities and side-cores.
### 2. Injection
Molten metal is injected into the die under high pressure. The pressure is maintained until the casting solidifies. This high-pressure injection is a key characteristic that distinguishes die casting from other casting methods.
Keyword: Die Casting
### 3. Cooling
The molten metal begins to cool and solidify once it enters the die cavity. The die cannot be opened until the cooling time has elapsed and the casting has solidified.
### 4. Ejection
After the predetermined cooling time has passed, the die halves are opened and the casting is ejected by the ejector pins. Any scrap metal, including the gate, runners, sprues, and flash must be removed from the casting, usually via a trimming process.
### 5. Trimming
During cooling, the material in the channels of the die will solidify attached to the casting. This excess material must be trimmed from the casting either manually or using a trimming press.
## Types of Die Casting
There are two main types of die casting:
### Hot-Chamber Die Casting
This process is primarily used for metals with low melting points such as zinc, magnesium, and lead alloys. The injection mechanism is immersed in a pool of molten metal.
### Cold-Chamber Die Casting
Used for metals with high melting points like aluminum and copper alloys. The molten metal is ladled into the cold chamber for each shot rather than being immersed in molten metal.
## Advantages of Die Casting
Die casting offers numerous benefits including:
- High production rates
- Dimensional accuracy and stability
- Smooth cast surfaces
- Thinner walls can be cast compared to sand and permanent mold casting
- Inserts can be cast-in (such as threaded inserts, heating elements, and high strength bearing surfaces)
- Reduces or eliminates secondary machining operations
- Long die life (especially for zinc die casting)
## Common Die Casting Materials
The most commonly used die casting alloys fall into the following categories:
Zinc Alloys
Zinc is the easiest metal to cast and offers high ductility, impact strength, and can be plated.
Aluminum Alloys
Aluminum alloys are lightweight while maintaining good strength and corrosion resistance.
Magnesium Alloys
Magnesium is the easiest alloy to machine and offers excellent strength-to-weight ratio.
Copper Alloys
Copper alloys offer high hardness and corrosion resistance along with good wear properties.
## Applications of Die Casting
Die cast parts are used in a wide variety of industries including:
- Automotive (engine blocks, transmission cases, cylinder heads)
- Aerospace (aircraft engine components)
- Consumer electronics (housing for computers, televisions)
- Household appliances (washing machine components, refrigerator parts)
- Power tools (drill housings, saw frames)