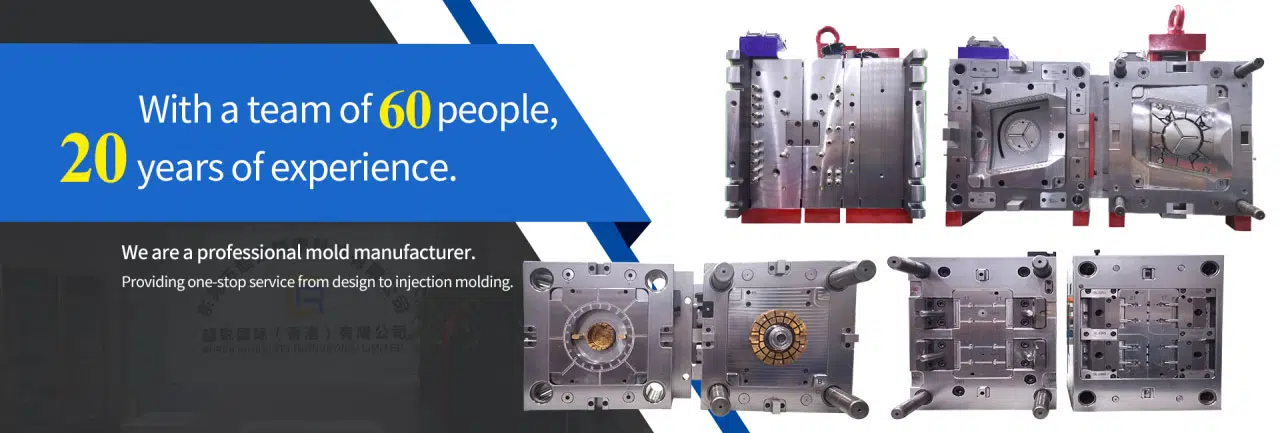
,文章长度在1000字左右
html
Surface Finishing Techniques for Enhanced Product Performance
Surface finishing plays a critical role in determining the performance, durability, and aesthetic appeal of manufactured products. From automotive components to medical devices, the right surface treatment can significantly enhance functionality while extending product lifespan. This article explores various surface finishing techniques and their impact on product performance.
The Importance of Surface Finishing
Surface finishing refers to the process of altering a product’s surface to achieve specific properties. These processes serve multiple purposes:
- Improving corrosion resistance
- Enhancing wear resistance
- Modifying electrical conductivity
- Creating decorative appearances
- Preparing surfaces for additional coatings
Without proper surface treatment, even the best-engineered products may fail prematurely due to environmental factors or mechanical stress.
Common Surface Finishing Methods
1. Electroplating
Electroplating involves depositing a thin layer of metal onto a substrate using electrical current. Common applications include:
- Chromium plating for automotive parts
- Gold plating for electronic connectors
- Nickel plating for corrosion protection
This process not only enhances appearance but also provides excellent protection against wear and environmental degradation.
2. Powder Coating
Powder coating applies a dry powder electrostatically, which is then cured under heat to form a protective layer. Benefits include:
Keyword: Surface Finishing
- Superior durability compared to liquid paints
- Environmentally friendly process (no solvents)
- Wide range of color and texture options
This method is particularly popular for outdoor equipment and appliances.
3. Anodizing
Primarily used for aluminum components, anodizing creates an oxide layer that:
- Improves corrosion resistance
- Enhances surface hardness
- Allows for color dyeing
The aerospace industry heavily relies on anodized aluminum for its combination of light weight and durability.
4. Mechanical Finishing
These physical processes include:
- Grinding and polishing for smooth surfaces
- Shot peening for stress relief
- Sandblasting for texture modification
Mechanical methods are often used as preparatory steps before applying other surface treatments.
Advanced Surface Finishing Technologies
1. Physical Vapor Deposition (PVD)
PVD creates thin film coatings through vacuum deposition. Characteristics include:
- Extremely hard, wear-resistant surfaces
- Excellent adhesion properties
- Environmentally clean process
This technology is widely used in cutting tools and medical implants.
2. Chemical Vapor Deposition (CVD)
CVD involves chemical reactions to deposit materials on substrates. Applications include:
- Semiconductor manufacturing
- Diamond-like carbon coatings
- High-temperature protective layers
This method produces coatings with exceptional purity and uniformity.
Selecting the Right Surface Finish
Choosing the appropriate surface treatment requires consideration of several factors:
Factor | Considerations</th Scroll Up |
---|