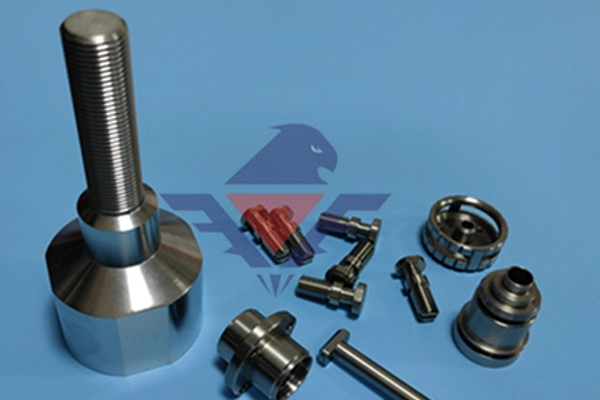
# Swiss Machining: Precision and Efficiency in Small Part Manufacturing
## Introduction to Swiss Machining
Swiss machining, also known as Swiss screw machining or Swiss turning, is a specialized manufacturing process that excels in producing small, high-precision parts with tight tolerances. Originating from Switzerland’s watchmaking industry in the late 19th century, this technology has evolved to become a cornerstone of modern precision manufacturing.
## How Swiss Machining Works
The Swiss machining process differs from conventional turning operations through its unique sliding headstock design. The workpiece is held in a collet and supported very close to the cutting tool by a guide bushing, which provides exceptional stability during machining. This setup allows for:
– Superior precision in long, slender parts
– Reduced vibration and deflection
– Simultaneous multiple operations
– Excellent surface finishes
## Key Advantages of Swiss Machining
### 1. Exceptional Precision
Swiss machines can maintain tolerances as tight as ±0.0002 inches (±0.005 mm), making them ideal for medical, aerospace, and electronics components where precision is critical.
### 2. High Efficiency
The ability to perform multiple operations in a single setup significantly reduces production time and increases throughput. Typical Swiss machines can incorporate:
– Turning
– Milling
– Drilling
– Threading
– Grooving
### 3. Material Savings
With the guide bushing supporting the material close to the cutting action, Swiss machining minimizes material waste compared to conventional turning methods.
## Applications of Swiss Machining
Swiss machining has found applications across various industries:
Medical Industry: Surgical instruments, implants, and dental components benefit from the precision and cleanliness of Swiss machining.
Keyword: Swiss Machining
Aerospace: Critical aircraft components requiring high strength-to-weight ratios and tight tolerances are often Swiss machined.
Electronics: Connectors, pins, and other miniature electronic components are efficiently produced using Swiss technology.
Automotive: Fuel injection components, sensors, and other precision automotive parts frequently utilize Swiss machining.
## Choosing the Right Swiss Machine
When selecting a Swiss machine for your manufacturing needs, consider these factors:
- Maximum part diameter capacity
- Bar feeder capacity
- Number of axes and tool stations
- Live tooling capabilities
- Control system features
## The Future of Swiss Machining
As manufacturing demands continue to push for smaller, more complex parts with tighter tolerances, Swiss machining technology is evolving with:
– Advanced multi-axis capabilities
– Improved automation integration
– Smarter CNC controls
– Enhanced tooling systems
– Better material handling solutions
## Conclusion
Swiss machining remains at the forefront of precision manufacturing, offering unparalleled accuracy and efficiency for small part production. Its continued evolution ensures it will remain a vital technology for industries requiring the highest levels of precision and quality in their components.